The most popular alloys are made of magnesium or aluminum. Aluminum or magnesium alloy is lighter than pure metal, but the strength is the same. They also look much better.
Steel is an alloy of iron and carbon and is the most commonly used material in wheel manufacturing. However, the term "aluminum alloy wheels" is used for wheels made of non-ferrous alloys (which do not contain iron). Therefore, when you hear the term "alloy wheel", it is most likely a wheel made of aluminum or magnesium.
Magnetic wheel"-the classic appearance of magnesium alloy
The original "magnetic wheels" were made of magnesium and were originally used in racing cars. Then, throughout the 1960s, they became very popular in standard production cars. In fact, if you are looking at a classic car, it may even have pure magnesium wheels. Unfortunately, pure magnesium is not ideal for wheels-it is prone to pits, cracks, and is more susceptible to corrosion.
Fortunately, it took a short time for engineers to start developing other alloy types, and at that time aluminum became more and more popular. Therefore, the term "magnetic wheel" is widely used to refer to any die-cast wheel made of any modern material (see below), including aluminum alloy wheels, all the way to bicycles, wheelchairs, roller skates and skateboards.
Low pressure die casting.
Die casting is a manufacturing process in which metal melts at high temperatures. Then, under low pressure, the metal is sealed, and then pressurized air or "mixed gas" presses the molten metal into the mold or "mold" along the straw-shaped filling tube.
There, the metal solidifies into a new form, and you have an alloy wheel. When done correctly, low pressure die castings produce better results than standard cast alloy wheels.
High pressure die casting.
The process is very similar to the low pressure die casting process. The mold is arranged in a large machine with high closing force. This forces the mold to close. Pour the molten magnesium into the filling tube (in this case, called the shot sleeve). The piston then pushes the metal into the mold very quickly under high pressure. After the magnesium is cured, open the mold and you will have a brand new magnesium die-casting wheel.
This method is much more economical than other methods, and reduces the price for consumers without affecting the corrosion resistance. However, they have poor ductility and are not as strong as low-pressure die-cast wheels.
High-performance forged wheels.
Forging can produce the best performance in aluminum alloy wheels, but it is a complex process that usually involves any combination of heating, rolling, applying high pressure and hammering. The result is that the molecular structure of the alloy becomes stronger and lighter at the same time. They also have higher "toughness" and "ductility" and aluminum wheels. The downside is that this is a labor-intensive process, so the cost is much higher.
Multi-piece aluminum alloy wheels.
Forged wheels can be forged into one, two or three pieces. If the grinding wheel is composed of two or three parts, you only need to assemble the grinding wheel into a finished product.
After-sales wheel.
If you are looking for lighter or more beautiful wheels to give your car a certain look or style, you can choose from a variety of alloy wheels, from standard 14-inch wheels to 28-inch large wheels.
However, research conducted by automobile and driver companies used alloy wheels of different sizes from 16 to 19 inches (41 to 48 cm). These wheels were all equipped with the same tire brand and model. The results showed that larger wheels would be lowered at the same time.
Acceleration and fuel economy. Therefore, in summary, there are many factors to consider when selecting the desired alloy.
Tools for repairing aluminum alloy wheels are also very important. Usually, wheel repair machine is your best choice. Our diamond cut wheel repair machine AWR902VP use diamond cutters, ruby probes and special soft jaws. diamond cutter: The diameter of the tip is 3mm, which is consistent with the size of ruby probe and improves the accuracy. Integrated blade, no vibration during cutting, high stability. As the originator of wheel repair machine in China, we have rich experience in this field. Looking forward to establishing long-term cooperative relationship with you and developing together.
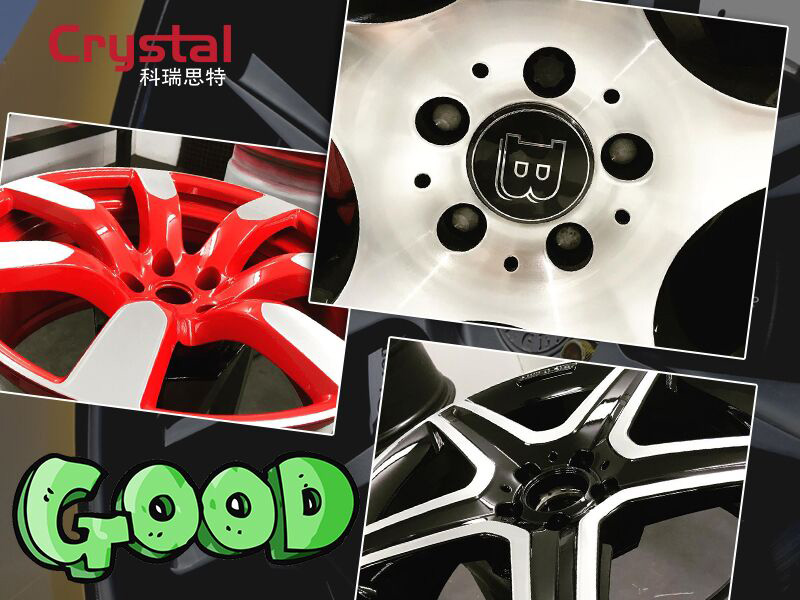