Wheels-hard-working components that need special looking after. Not only can their appearance make or break the look of a vehicle but their condition can also significantly impact on resale values. Not surprising then, that a considerable amount of product advice calls the UF Team answer, involve the correct use of wheel cleaners and sealants. With so many different types of wheel finishes on the market and with such a myriad of products available, determining the right one for your wheels can be tricky. In this article, we look at some of the popular types of wheel finish and highlight the differences which determine the best practices for keeping them looking “as new”.
These days, many cars have alloy wheels, made from either aluminium or magnesium mixed in with traces of other metals to give them greater strength. Aluminium alloy wheels are found on most modern cars; magnesium alloys can be more brittle than aluminium alloy wheels and as such are typically found on high-end sports cars or race cars where this is outweighed by being lighter, a typical “Mag Alloy” wheel weighs between 5-9kg.
Types of alloy wheel finishes vary greatly. Some of the most popular are:
Painted & Lacquered: standard for most cars, e.g. Audi, BMW, Ford, etc.
Powder Coated: a more durable finish
Anodised: used on some aftermarket custom wheels and lightweight race wheels
Diamond Cut: high shine look commonly used by manufacturers to highlight their top of the range models
Split Rims: often seen on Porsche, BMW and VW, very popular in the custom scene
Chrome: mostly found on classic cars
Diamond Cut wheels are first painted in the selected colour and then baked in an oven. Once dry the wheel is mounted on a wheel repair machine (computer numerical controlled) so that the face of the wheel can be machined to achieve the metallic diamond cut pattern. The wheels are then sprayed with an Acrylic Lacquer to finish the look.
In the initial condition, the wheel surface is so smooth that no protective lacquer can adhere to it unless there is some surface stripping done. During the process of diamond cutting, the wheel is mounted on a lathe machine. As the wheel rotates on the machine, a diamond cutter grazes the surface of the allow to remove a very thin layer that was affected by the stress encountered by the wheel.
By the diamond cutting process, it is possible to prepare the surface for polishing and finishing that enhances the wheel aesthetics, which lasts for a longer time. Applying lacquer to the freshly cut surface protects the wheel for damages for some time.
For the best results, the experts recommend repeating the diamond cutting process 2-3 times. However, it is important not to remove too many layers from the wheel surface, which can become very thin and become vulnerable to cracks and damages.
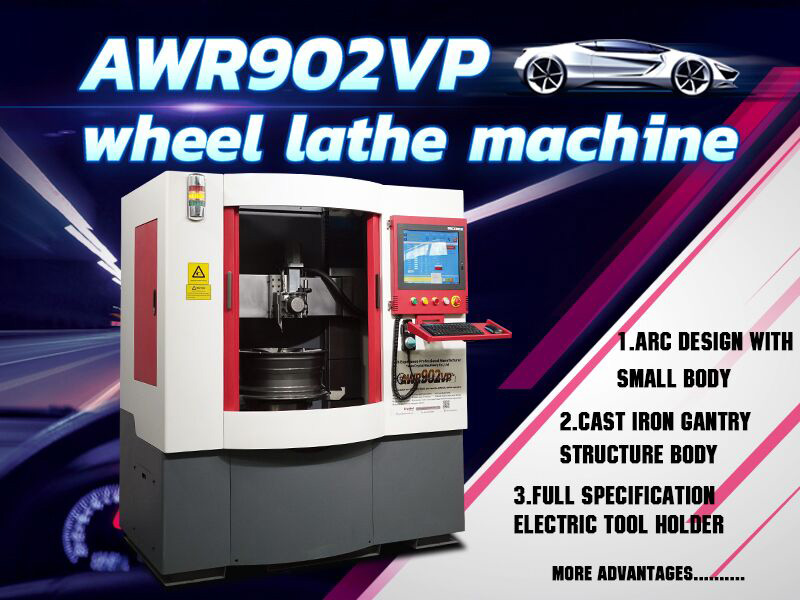